What is Porosity in Welding: Typical Resources and Reliable Solutions
The Scientific Research Behind Porosity: A Comprehensive Guide for Welders and Fabricators
Recognizing the detailed mechanisms behind porosity in welding is crucial for welders and makers aiming for impressive workmanship. From the composition of the base materials to the intricacies of the welding procedure itself, a plethora of variables conspire to either worsen or ease the existence of porosity.
Comprehending Porosity in Welding
FIRST SENTENCE:
Evaluation of porosity in welding discloses vital understandings into the honesty and quality of the weld joint. Porosity, defined by the visibility of cavities or voids within the weld metal, is an usual concern in welding procedures. These gaps, otherwise effectively attended to, can endanger the architectural integrity and mechanical residential or commercial properties of the weld, bring about possible failings in the ended up product.

To find and measure porosity, non-destructive screening methods such as ultrasonic testing or X-ray assessment are usually used. These techniques enable the recognition of inner issues without endangering the honesty of the weld. By analyzing the dimension, form, and distribution of porosity within a weld, welders can make informed choices to boost their welding procedures and accomplish sounder weld joints.
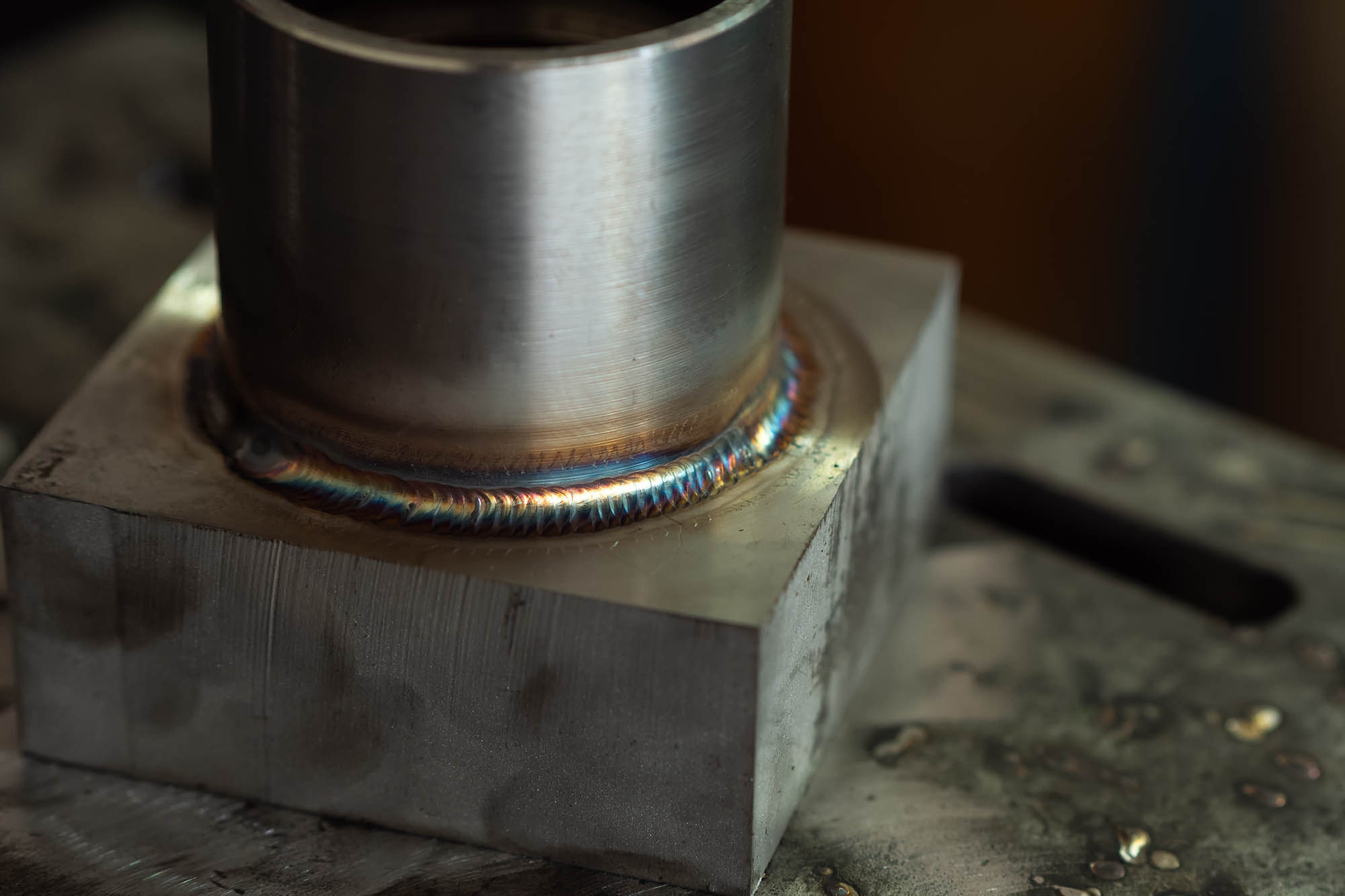
Elements Affecting Porosity Development
The event of porosity in welding is affected by a myriad of aspects, varying from gas shielding efficiency to the intricacies of welding specification setups. One critical aspect adding to porosity formation is inadequate gas securing. When the shielding gas, commonly argon or carbon dioxide, is not efficiently covering the weld swimming pool, atmospheric gases like oxygen and nitrogen can infect the molten steel, bring about porosity. In addition, the cleanliness of the base products plays a significant function. Impurities such as rust, oil, or dampness can evaporate during welding, producing gas pockets within the weld. Welding criteria, consisting of voltage, present, travel speed, and electrode type, additionally effect porosity formation. Using incorrect settings can generate too much spatter or heat input, which consequently from this source can cause porosity. The welding method utilized, such as gas steel arc welding (GMAW) or secured steel arc welding (SMAW), can influence porosity development due to variations in heat distribution and gas protection. Recognizing and regulating these variables are vital for decreasing porosity in welding procedures.
Results of Porosity on Weld Top Quality
The visibility of porosity also deteriorates the weld's resistance to deterioration, as the trapped air or gases within the spaces can respond with the surrounding environment, leading to deterioration over time. In addition, porosity can hinder the weld's capability to hold up against pressure or effect, more jeopardizing the overall high quality and dependability of the bonded framework. In crucial applications such as aerospace, vehicle, or architectural buildings, where safety and toughness are extremely important, the harmful effects of porosity on weld high quality can have extreme repercussions, stressing the significance of decreasing porosity via correct welding methods and procedures.
Methods to Decrease Porosity
In addition, using the suitable welding criteria, such as the correct voltage, present, and travel rate, is crucial in protecting against porosity. Preserving a constant arc length and angle during welding also assists decrease the possibility of porosity.

Using the suitable welding method, such as back-stepping or employing a weaving motion, can also help distribute heat evenly and reduce the chances of porosity formation. By implementing these strategies, welders can successfully decrease porosity and generate high-grade bonded joints.

Advanced Solutions for Porosity Control
Applying innovative innovations and innovative methods plays a crucial function in achieving superior control over porosity in welding procedures. One innovative remedy is using innovative gas mixes. Protecting gases like helium or a mix of argon and hydrogen can see this website assist lower porosity by giving better arc stability and enhanced gas protection. Additionally, using Full Report advanced welding strategies such as pulsed MIG welding or changed environment welding can likewise aid reduce porosity issues.
Another advanced service includes making use of sophisticated welding equipment. For circumstances, making use of equipment with built-in functions like waveform control and innovative source of power can improve weld top quality and lower porosity risks. In addition, the application of automated welding systems with exact control over criteria can significantly minimize porosity defects.
In addition, including innovative surveillance and examination modern technologies such as real-time X-ray imaging or automated ultrasonic screening can assist in detecting porosity early in the welding procedure, enabling prompt restorative actions. In general, integrating these advanced remedies can substantially boost porosity control and improve the overall quality of welded parts.
Final Thought
Finally, understanding the scientific research behind porosity in welding is necessary for welders and producers to create premium welds. By recognizing the aspects influencing porosity development and carrying out techniques to decrease it, welders can boost the general weld quality. Advanced options for porosity control can even more boost the welding process and ensure a solid and reputable weld. It is essential for welders to constantly educate themselves on porosity and carry out best methods to achieve optimal outcomes.